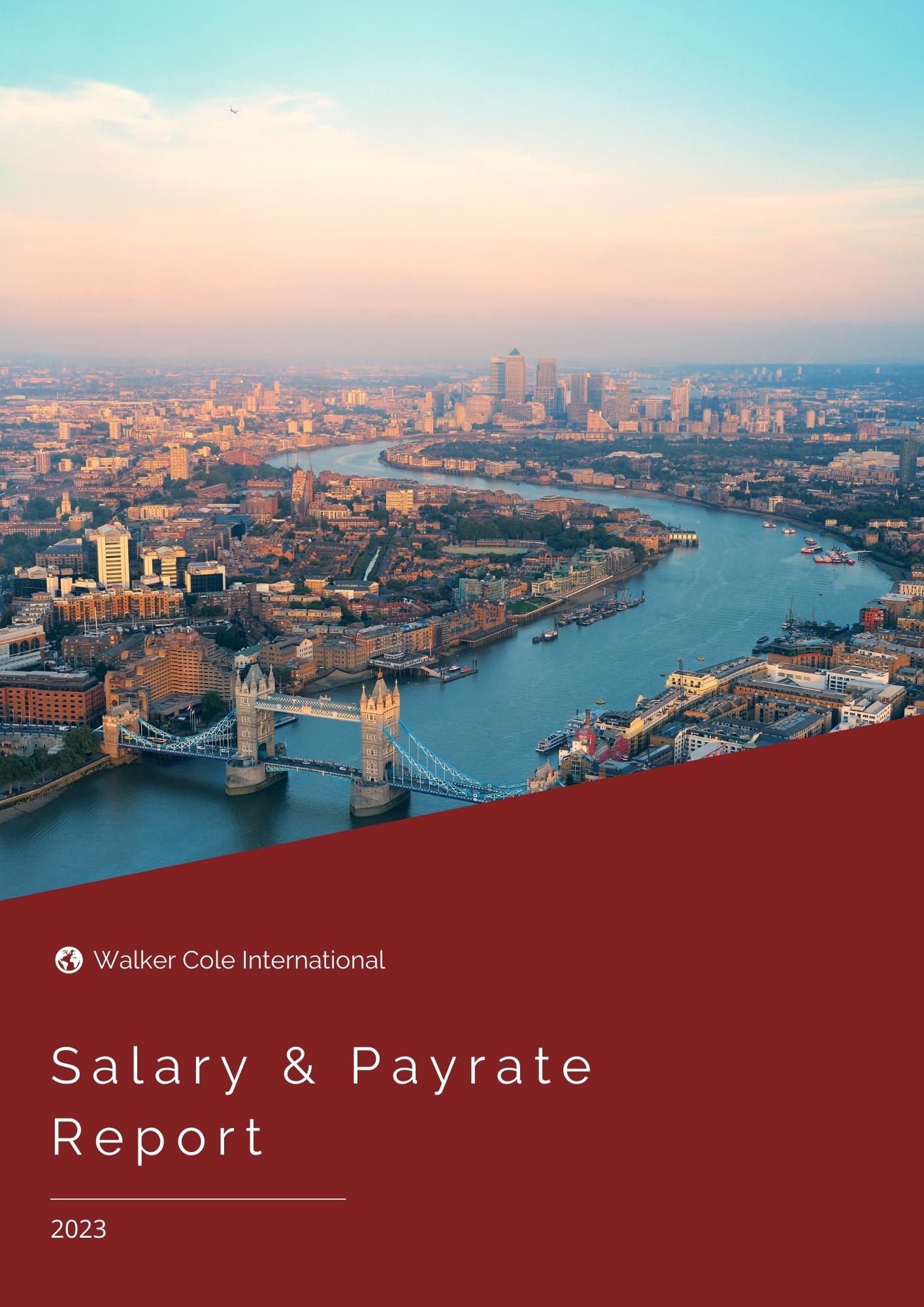
Drop off your CV
Lorem ipsum dolor sit amet, consectetur adipiscing elit. Aliquam gravida odio at semper semper or get in touch
Quality Assurance White Paper – Summer 2022Quality Assurance of products provided to patient...
Quality Assurance White Paper – Summer 2022
Quality Assurance of products provided to patients is one of the most important disciplines in the modern pharmaceutical industry. In this area the responsibility for ensuring that any products released adhere to the relevant compliance regulations falls on the Qualified Person (QP).
As the pharmaceutical industry continues to evolve and change with new medicinal products and therapies such as ATMP’s, along with the changing attitudes to work in the post pandemic world, Walker Cole International sought the opinion of practicing QP’s on several 5key issues that affect how this pivotal role is performed.
• How can hybrid working be incorporated to enable someone to effectively perform the duties of a Qualified Person?
Hybrid working is becoming one of the most important topics on the agenda of candidates when searching for a new role, The MHRA addressed this during the pandemic with the publishing of its “Work From Home Guidance”, but the question remains how effective this will be as we exit the pandemic.
The responses to this white paper reveal some common areas of consideration for this issue when it comes to the role of the Qualified Person.
1) No QP role can be fully remote, there was unanimous agreement that QP’s need to have a level of on-site presence, the exact amount depends on specific conditions (number of QP’s on the license, dosage form, manufacturing vs virtual business etc). Even for virtual businesses a QP should be involved in the Supplier Audit programme and visit manufacturing facilities on a regular basis. Some activities such as incident management and self-inspection audits require a physical presence.
2) Hybrid working is facilitated more effectively with up-to-date technology and processes, there are some aspects of a QP’s role that can be performed remotely using systems such as SharePoint/DocuSign as well as an effective eQMS which can enable Quality Issues to be raised in real-time. In addition, a key factor to a QP’s role is the understanding of a site’s practice and working through meetings/interactions with other business leaders e.g. Production/Supply Chain, effective video conferencing tools can ensure that on-site presence is not always required for this to occur.
• What are the implications of a remote release process on GMP compliance?
Remote release processes are already commonplace in many pharmaceutical businesses, particularly virtual organisations where the QP is certifying a batch that has been manufactured overseas by a third party/CMO.
A key issue highlighted with remote release processes is the lack of in person checks or inspections, i.e relying on photographs of products during physical inspection. A key aspect of a QP’s role is to make judgements based on the information available to them, and there is an argument that more information is gathered by being present on site than during a virtual release process. The fact that this can be avoided with the QP’s presence on a manufacturing site links to some of the discussion points from the hybrid working question and seems to highlight the need where possible that a QP spends enough time on site understanding the processes and personnel involved in the manufacture of products.
Unanimously though the most important factor for ensuring that a remote release process has no impact on GMP compliance comes from the effectiveness of digital/eQMS systems. Many businesses now have the systems in place to electronically perform the release process remotely however it is essential that a QP has access to all necessary documentation (through an effective QMS) and appropriate SOPs in place governing the release process.
Again, the development and deployment of an effective Electronic QMS gives an accurate overview of activities on site and is essential to ensuring compliance is maintained.
Interestingly some of the responses highlighted that the remote certification process is being used by some companies as an activity that can be defined as one that is to be performed by QP’s while working remotely, leaving on-site QP’s to action other tasks that ensure GMP compliance is maintained.
• Do you believe there is a maximum number of licenses that it is feasible for a contract QP to operate on at any one time? If so, how many?
The topic of a maximum number of licenses that it is feasible for a contract QP to be on prompted the largest difference of opinion amongst the QP community. 44% of responses felt that 3 licenses were the maximum number that is feasible for a contract QP to be named on. There was a consensus that the MHRA would intervene and ask questions if a QP were to be named on 4 licenses or more. Interestingly 21% of QP’s believed that 4 licenses could be feasible however this was with additional caveats requiring an effective QMS system to be in place and an experienced QA Batch Release Team who could support the QP in their duties.
71% of all responses believed that 2 or 3 licenses would be the appropriate number to be named on. Key considerations raised include the dosage form being dealt with, with products such as ATMP’s, particularly those still being developed, or other complex dosage forms requiring additional scrutiny to ensure compliance is being maintained. Established traditional routine manufacture of products enables a QP to safely be named on multiple licenses.
It is important to note at this stage that the role of a contract QP can differ slightly from a permanent QP in terms of the level of influence they have in the day to day running of a business. There are however some non-negotiable elements that a QP must have oversight of to ensure they can execute their role effectively.
Key Takeaways/Reflections
This work has emphasised the important topic that the role of the QP is not only dependent on the individual performing the role of a Qualified Person, but the personnel and processes associated with the manufacture of a product. Without effective Quality Governance processes and trained colleagues who appreciate the importance of compliance, it is challenging to ensure compliance is maintained.
The role of a QP when performed effectively expands beyond that of a pure batch certification role; it is an instrumental role in the site’s operations requiring strong relationships at a leadership level with internal stakeholders and departments. It is also clear that the digital age of technology is continuing to revolutionise the way in which QP’s can perform their duties.